By Jim Dickson | Contributing Editor
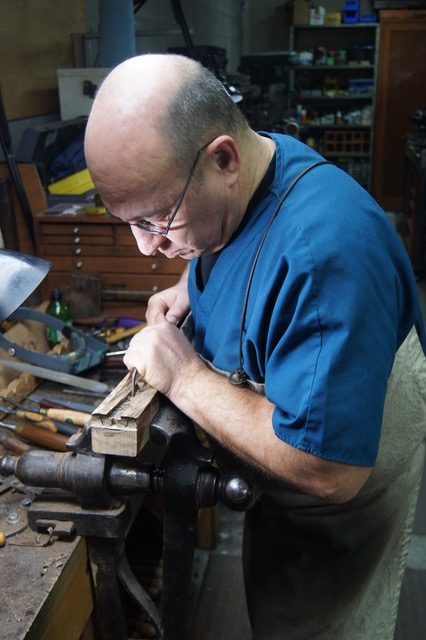
When you have a Purdey, Dickson, Holland & Holland, or other Best Quality gun and need a new stock you have a bit of a problem.
It’s difficult and expensive to send the gun back to England for restocking and then have it returned. Reports of Heathrow Airport personnel in London deliberately wrecking guns in transit do nothing to reassure you about the safety of this venture.
Guns stocks can break, and a new owner needs the gun stocked to fit his measurements, not the previous owner’s. You can never get the full benefits of a Best Quality gun without having it stocked to your measurements. These are taken with a try gun at the gunmaker’s establishment or a shooting school in the British Isles. Every possible dimension is measured to a 1/16th of an inch in order to produce a gun that will be unerringly pointed exactly where you are looking so that it can be fired the instant it is cheeked without you ever seeing the gun barrels and without missing the target.
Often the old stock can be altered to fit the new owner. Other times a completely new stock must be made from scratch. Either way only an experienced workman well established in the Best Quality gun making trade should be trusted with a gun worth 5 or 6 figures.
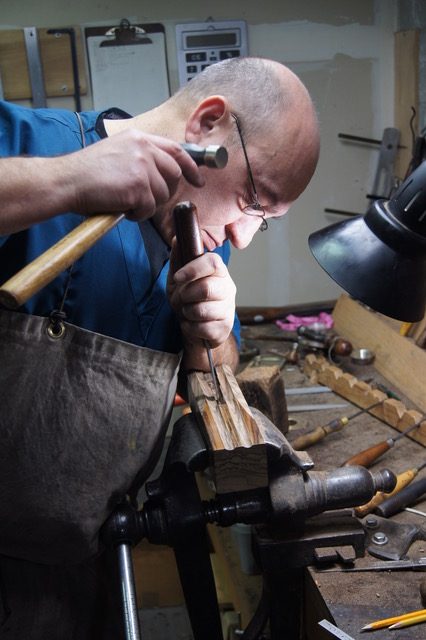
Paul Hodgins is such a man. He served his apprenticeship at the famed Holland & Holland gunmakers in London and stayed on as a stocker for their Best Quality guns. It is important to realize that the degree of artistry, fit, and finish of a Best Quality gun far exceeds anything that can be accomplished by machines and this workmanship requires a long and demanding apprenticeship in the trade. Paul’s story should give you some insights into this demanding trade.
Hodgins was born in 1957 in Greenford, Middlesex, UK. His family moved to Buckinghamshire in 1960 and his mother still lives there.
In 1973 when Paul was 16 he began a 5-year apprenticeship as a stocker at Holland & Holland where he was one of seven new apprentices that year. Holland & Holland had set aside a part of one of the shops as the “Apprentice School” to train them under Stan Robinson, a machine shop engineer for the first year. He taught them to use files, hacksaws, milling machines, drill presses, lathes, off-hand grinding, and heat treating. Periodically an actioner would come to teach one aspect of gun making at a time such as fitting extractors to the barrels.
All the time they were learning to use hacksaws, files, etc. they were using those skills to build the gunmaker’s tools they would be using the rest of their working lives. The first year was to teach them enough that they could work smoothly as they transitioned to the specialty they chose. They needed to know all about the specialized tools, nuances, and idiosyncrasies that go with the trade.
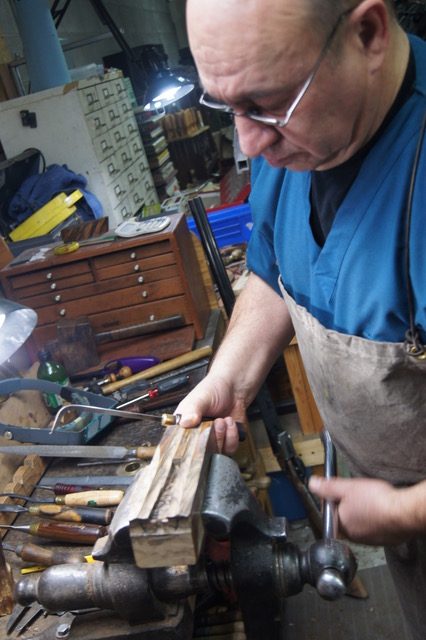
Paul chose to enter the stocking shop under the guidance of the foreman, Angel Rego from Spain. He started making fore-ends for an old scrapped sidelock. Next, Rego had Hodgins making stocks for that old gun. This was all very good and necessary practice. When he became sufficiently proficient he was then tasked to restocking boxlock guns for clients and when he got the hang of those they moved him on to restocking sidelocks. In his third year they began letting him work on new Holland and Holland Royal grade guns. He still had to do restocking as well until a new apprentice was competent to take over that duty.
There is a great deal of metal work to do when stocking a new gun. Trigger blades have to be filed and shaped to accommodate the sears and the safety. The safety bar is filed down to reduce the length in relation to the triggers. The over long sear tails are ground down so as to almost meet in the middle but not touch each other while being hung slightly over the trigger blades. This whole process is termed “Hanging the triggers.”
Then during the inletting part of stocking the breech pin was used as a guide as to how much steel could be removed in the final fitting of the sears and safety arrangement. There needed to be the slightest of freedom of movement between the sear and trigger relationship when the safety was OFF but less when the safety was ON. All this was finalized during the finishing operation in the finishing department. When the stockers had done their part of the job the mechanism only needed to work at this junction. Stockers also had to file the draught angles onto the sides of the top strap, trigger plate, and lock plates.
Next came the fore part. It was the stockers job to file to shape the fore end loop that’s attached to the barrel. This included the height and the hook portion that the fore end bolt fits to. It was just a blank piece of steel on the barrels when it came to them. They then filed and fitted the “Snap work” to fit the loop, filed on the draught angles to the tube, the iron and bolt for stocking.
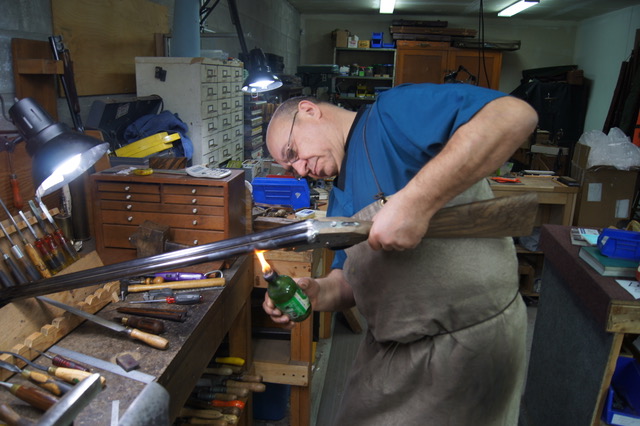
At this stage the wood was left a little thicker with no drop points shaped on and was known as being “In the rough” whereupon it was sent to the range for regulating the chokes. Upon its return it was now time for final shaping or “Making off” -shaping down to the required dimensions, cutting in the drop points, and smoothing and wet and drying where the stock and fore end were sanded starting with the coarse 100 grit and finishing with 180 grit all the while applying a solution of diluted oxalic acid between sandings and drying over a soft flame. This would raise the grain making the wood prickly until after the sandings were finished. This process has sometimes been called “whiskering” by some stock builders and wood workers.
Then no more grain would rise unless the wood was filed for some reason which would mean it would be back to the “Wet & dry” operation. At this stage a gold oval was fitted if desired.
Upon finishing the “Wet & dry” the stockers applied a coating of red oil, this is raw linseed oil with alkeanet root soaking in it with the red color from the root leaching into the oil turning it a deep red. The excess was wiped off and when dry to the touch the stock would be sent to the Finishing Department. The stock would be about 1/16 of an inch too long as final length and balance was the finisher’s job. Hodgins began to do finishing work a bit later.
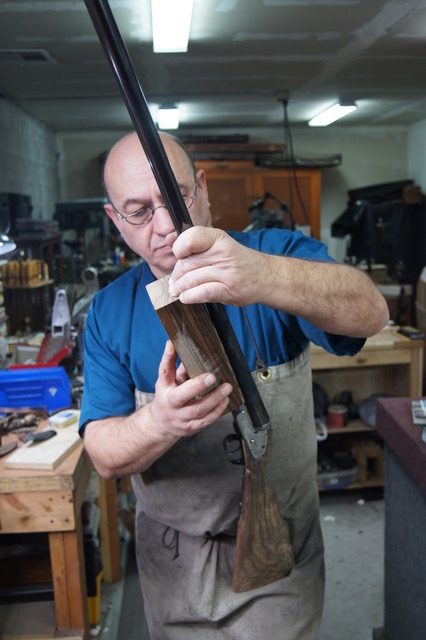
When stocking single trigger guns, the barreled action would arrive in the stocking shop with the components of the trigger mechanism left in their small block or blank forms but nevertheless mounted to the trigger plate. After stocking the gun, including the fore end, it was sent back to the action shop where the trigger components were filed and fitted to shape in-situ with the stock so that all would work properly. Often the actioner working on the gun would come up to the stocker to have him remove any tiny amounts of wood that were impeding the function of the trigger mechanism he was filing and fitting. Once he got it working it was off to the range and ultimately to the finishing department to finely tune everything, and prepare it for the customer.
After completing his apprenticeship Paul was assigned to stocking new Holland & Holland Royal grade double shotguns and rifles with a few bolt action guns thrown in. He spent time with other gunmakers learning more skills such as re-jointing.
Upon leaving Holland & Holland Paul set up a small shop where he did restocking primarily for the gun trade. In 1982 he went to Canada where he worked for Frank Malin, Gunmakers in Ontario. In 1983 he came to Texas where he worked in a gun shop that dealt in fine guns for 5 years until the shop closed. After that he branched out on his own.
These days Paul stays busy stocking guns and doing some metal work repair. We are extremely fortunate to have such a highly trained and skilled stocker in this country. Far too few workmen at the bench in the British gun trade come to these shores and the ones that do shine like rare jewels. It is the height of foolishness to entrust a valuable Best Quality gun to anyone outside of the Best Quality gun trade. He can be reached at:
Paul Hodgins
Hodgins Gunstocks
P.O. Box 3546
Logan, Utah 84323
435-753-2796